新形勢(shì)下工廠設(shè)備管理的5大誤區(qū)與對(duì)策
在全球智能制造的浪潮下,我國(guó)制造業(yè)積極升級(jí)轉(zhuǎn)型,自動(dòng)化、數(shù)字化、網(wǎng)絡(luò)化水平大大提高,生產(chǎn)設(shè)備日益走向集成化、智能化,設(shè)備數(shù)據(jù)可視化程度顯著提高、操作上更加簡(jiǎn)單。但伴隨而來的是設(shè)備的維護(hù)修理難度加大、維護(hù)成本提高,設(shè)備維護(hù)保養(yǎng)的作用也越來越凸顯。但在許多企業(yè)我們看到,企業(yè)花費(fèi)巨資上馬了非常先進(jìn)的設(shè)備,而設(shè)備的管理維護(hù)、人員知識(shí)結(jié)構(gòu),仍停留在傳統(tǒng)層面:數(shù)采基本靠筆,處理基本靠人,分析基本靠猜(經(jīng)驗(yàn))??梢哉f是買來了4.0的設(shè)備,延續(xù)著1.0的管理。
從設(shè)備資產(chǎn)效益產(chǎn)出角度看,我國(guó)制造業(yè)的設(shè)備綜合效率的提升空間巨大。據(jù)統(tǒng)計(jì),我國(guó)大部分離散制造業(yè)的OEE在60%左右,距離發(fā)達(dá)國(guó)家至少還有10%-20%的提升空間。同時(shí),很多工廠對(duì)設(shè)備維護(hù)和保養(yǎng)的精細(xì)化管理不夠重視,這當(dāng)中造成的異常停機(jī)和備件浪費(fèi)等隱性損失,更是巨大的浪費(fèi)。在當(dāng)前疫情沖擊、全球化局勢(shì)不確定性進(jìn)一步增加的形勢(shì)下,這些效益改善空間,都可以為企業(yè)的生存、增強(qiáng)競(jìng)爭(zhēng)力提供寶貴的機(jī)會(huì)。
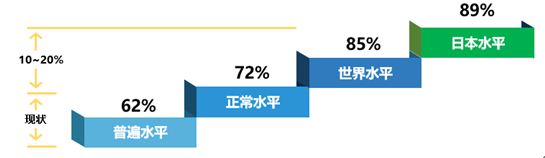
圖:離散制造業(yè)OEE現(xiàn)狀評(píng)估
如何構(gòu)建面向新型設(shè)備的管理能力,是當(dāng)前制造業(yè)面臨的一個(gè)問題和挑戰(zhàn)。在這個(gè)過程中,我們總結(jié)了大家常常存在的5個(gè)誤區(qū),并給出了對(duì)應(yīng)的策略建議,希望可以幫助企業(yè)少走一些彎路。
第一,重硬輕軟
大部分企業(yè)新建工廠或者新購(gòu)買的設(shè)備,只重視硬件的驗(yàn)收交接,忽視了軟件的維護(hù)保養(yǎng)、校準(zhǔn)標(biāo)準(zhǔn),沒有明確要求設(shè)備數(shù)據(jù)采集接口和設(shè)備數(shù)據(jù)所有權(quán)的訴求。根據(jù)工信部相關(guān)數(shù)據(jù)最新統(tǒng)計(jì),目前我國(guó)企業(yè)生產(chǎn)設(shè)備的數(shù)字化率平均為47%,關(guān)鍵工藝的數(shù)控化率51%,關(guān)鍵設(shè)備聯(lián)網(wǎng)率41%。 嵌入式軟件、人機(jī)界面、數(shù)據(jù)監(jiān)測(cè)模型、管理平臺(tái)都是新型設(shè)備的重要組成部分,都應(yīng)是新型設(shè)備管理的范疇。從筆者進(jìn)行工業(yè)互聯(lián)網(wǎng)相關(guān)項(xiàng)目的經(jīng)驗(yàn)看,設(shè)備的數(shù)據(jù)采集受制于工業(yè)現(xiàn)場(chǎng)協(xié)議眾多、原廠不開放不支持、設(shè)備數(shù)據(jù)不確權(quán)等原因,設(shè)備數(shù)采仍然是生產(chǎn)現(xiàn)場(chǎng)數(shù)字化推進(jìn)中成本最高的組成部分之一。比如我國(guó)許多SMT產(chǎn)線,貼片機(jī)本身精度很高、節(jié)拍很快、良率也都在99%以上了,單純?cè)倏渴止ふ{(diào)試,很難再提升了。許多工廠期望能將貼片機(jī)的數(shù)據(jù)實(shí)時(shí)數(shù)采和分析,解決自動(dòng)叫料接料問題,改善拋料問題。但目前動(dòng)輒數(shù)萬的數(shù)采license費(fèi)用,讓許多工廠望而卻步。
因此,工廠在設(shè)備采購(gòu)環(huán)節(jié)就提前考慮,將相關(guān)要求加入商務(wù)條款,可以為以后設(shè)備制程詳細(xì)數(shù)據(jù)的采集和分析優(yōu)化做好準(zhǔn)備。
第二,生產(chǎn)為重,不壞不修、不停不管
在大部分工廠,特別是離散制造業(yè),都是生產(chǎn)是老大,設(shè)備只是保障部門,只要還能運(yùn)轉(zhuǎn),就不會(huì)停產(chǎn),這導(dǎo)致設(shè)備維護(hù)改善的時(shí)間和資金投入嚴(yán)重不足,設(shè)備部也陷入了四處救火、窮于應(yīng)付的被動(dòng)惡性循環(huán)。究其原因,是因?yàn)闆]有從工廠端到端視角看設(shè)備停機(jī)的損失。在設(shè)備初期征兆的時(shí)候介入維護(hù),遠(yuǎn)比造成停機(jī)后再維護(hù),造成的損失和投入成本要小的多。如下圖,某機(jī)床通過振動(dòng)分析,可以看到10月18日振動(dòng)加速度峰值觸發(fā)早期預(yù)警閾值,但是由于生產(chǎn)計(jì)劃問題,沒有停機(jī)維護(hù);10月22日機(jī)床主控系統(tǒng)觸發(fā)故障,不得不停機(jī)過10個(gè)小時(shí)維修和更換軸承,維修后,振動(dòng)恢復(fù)正常水平,但巨大損失已經(jīng)造成。
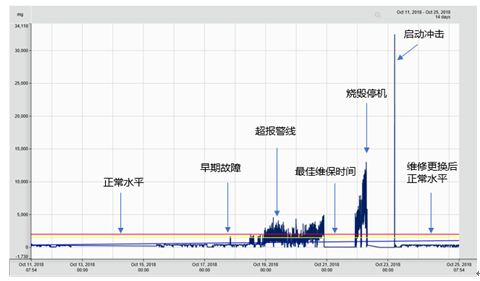
圖:通過振動(dòng)分析可以監(jiān)測(cè)大部分機(jī)械故障
從設(shè)備管理大體經(jīng)過的4個(gè)主要階段來看,從1.0的糾正性維護(hù)(CM),到2.0預(yù)防性維護(hù)(PM)、3.0的可靠性維護(hù)(RCM)、4.0的預(yù)測(cè)性維護(hù)(PHM),本質(zhì)上都是以設(shè)備健康管理(EHM)為中心,從“治已病”到“治未病”的進(jìn)化過程。通過EHM,設(shè)備健康狀態(tài)不再是被簡(jiǎn)單的劃分為正常、異常。我們可以通過新技術(shù)、新工具,分析積累的基礎(chǔ)數(shù)據(jù),評(píng)估出設(shè)備的亞健康狀態(tài),此時(shí)提前介入可以大大減少設(shè)備維護(hù)成本。例如,東智EHM給設(shè)備維護(hù)工程師配備帶有振動(dòng)傳感器的智能點(diǎn)檢儀,就像給醫(yī)生配了“智能聽診器”一樣,通過數(shù)秒的監(jiān)測(cè)振動(dòng)頻譜,結(jié)合內(nèi)置的頻譜分析模型,就可以準(zhǔn)確、快速的判斷出設(shè)備健康狀態(tài)、故障征兆原因,對(duì)故障輔助診斷起到重大作用。這樣設(shè)備人的職責(zé)從原來的壞了維修,更多的轉(zhuǎn)向如何保障設(shè)備健康運(yùn)行的專業(yè)維保維護(hù)工作,進(jìn)入良性循環(huán)。
第三,設(shè)備問題就是設(shè)備部的事情
雖然TPM已經(jīng)推行了多年,但許多管理者觀念和行動(dòng)上,還是認(rèn)為設(shè)備出了問題,就是設(shè)備部的事情,導(dǎo)致生產(chǎn)部門對(duì)設(shè)備的故障不關(guān)心,對(duì)影響產(chǎn)量、質(zhì)量的設(shè)備維護(hù)不重視。設(shè)備維護(hù)工程師也往往低地位、低薪酬,自嘲為看門狗和替罪羊:節(jié)假日,別人可以休息,他們卻不能離開,因?yàn)檫@正是維修設(shè)備的好時(shí)機(jī);凡是出了問題,無論是設(shè)備停機(jī),生產(chǎn)停產(chǎn),還是質(zhì)量事故,都會(huì)與設(shè)備相關(guān),設(shè)備人員幾乎永遠(yuǎn)是背鍋的。為此,整個(gè)設(shè)備部成了優(yōu)秀的人最不愿意去的地方。這種惡性循環(huán)現(xiàn)象,需要生產(chǎn)管理者身體力行樹立正確的設(shè)備管理理念,構(gòu)建生產(chǎn)為主體的全員自主維保體系。只有生產(chǎn)部門管理者重視起來了,全體生產(chǎn)設(shè)備操作者才能改變對(duì)設(shè)備漠不關(guān)心的態(tài)度,才能有效進(jìn)行設(shè)備保養(yǎng)。而這個(gè)光靠設(shè)備部是玩不轉(zhuǎn)的。
工廠可以通過引入設(shè)備健康管理EHM解決方案,構(gòu)建全員自主維護(hù)保養(yǎng)體系,實(shí)現(xiàn)操作工的日常自主點(diǎn)檢和保養(yǎng)、設(shè)備部的專業(yè)點(diǎn)檢、設(shè)備故障掃碼報(bào)修、掃碼維護(hù)、維保工單自主搶單、維修效果用戶評(píng)價(jià)、績(jī)效競(jìng)比等功能和機(jī)制,幫助工廠實(shí)現(xiàn)TPM的自運(yùn)轉(zhuǎn)。
第四,將設(shè)備維護(hù)當(dāng)做成本中心,忽視了冰山下的損失
許多管理者認(rèn)為設(shè)備零故障是不可實(shí)現(xiàn)的,企業(yè)在遇到困難需要削減成本時(shí),很多情況是拿設(shè)備維修費(fèi)用開刀,甚至提出讓維修預(yù)算每年遞減百分之幾的目標(biāo)。從傳統(tǒng)財(cái)務(wù)角度看,維修所消耗的資金一般被定義為成本和費(fèi)用。其實(shí)早在30年前,德國(guó)召開歐洲維修團(tuán)體聯(lián)盟國(guó)際會(huì)議時(shí),就提出“維修——為了未來的投資“的主題。作為投資,就需要有清晰的投入產(chǎn)出。維修的投入是設(shè)備日常維護(hù)所投入的人工費(fèi)、各類防護(hù)費(fèi)、備件費(fèi)、設(shè)備管理相關(guān)系統(tǒng)。產(chǎn)出是什么呢?是由于設(shè)備維護(hù)不足、設(shè)備管理不善,帶來的設(shè)備停機(jī)、精度或者質(zhì)量缺陷帶來的損失。如果對(duì)這些損失的價(jià)值誤判,則容易扼殺設(shè)備維護(hù)技術(shù)和管理體系的改善性投入。
筆者曾經(jīng)服務(wù)過一家大型工廠,設(shè)備部要上馬EHM項(xiàng)目,實(shí)現(xiàn)設(shè)備的數(shù)據(jù)采集和監(jiān)控,同時(shí)通過移動(dòng)化的巡點(diǎn)檢,實(shí)現(xiàn)設(shè)備的報(bào)修和維護(hù)過程,形成設(shè)備的故障樹記錄。在核算投入產(chǎn)出的時(shí)候,屢屢被財(cái)務(wù)挑戰(zhàn),過不了關(guān)。他們理解降低設(shè)備停機(jī)1小時(shí)的價(jià)值,僅僅是這1小時(shí)涉及到的員工的人工成本。這樣算下來,價(jià)值產(chǎn)出太低,許多設(shè)備改善項(xiàng)目沒法上馬。而且這樣的項(xiàng)目?jī)r(jià)值核算標(biāo)準(zhǔn),直接打壓了工廠精益革新的積極性。設(shè)備停機(jī)一小時(shí)的損失,要從工廠視角端到端的去衡量整體,這里面其實(shí)包括了產(chǎn)能損失的機(jī)會(huì)成本,即1小時(shí)的產(chǎn)品產(chǎn)值損失,才是這個(gè)工廠真正的損失。這樣算下來,工廠許多可以改善停機(jī)、改善浪費(fèi)、現(xiàn)場(chǎng)精益類的小改小革的項(xiàng)目,都可以得到了合理的開展,能激發(fā)起基層員工的創(chuàng)新積極性,也確實(shí)能給工廠帶來實(shí)實(shí)在在的效益。
在實(shí)際操作中還存在一個(gè)問題,就是備件的更換很大程度上掌握在維修工手上,存在著許多“人為掌握”更換的因素。維修人員大都靠經(jīng)驗(yàn)判別備件損壞程度,對(duì)懷疑有故障的零部件,通常為了減少背責(zé)、或降低工作難度,即使還可以用也會(huì)更換成新的,可能存在過度維護(hù)的隱性浪費(fèi)。比如在TCL華星光電,由于大部分都是進(jìn)口件,每年備件費(fèi)用就數(shù)億,通過東智設(shè)備健康管理EHM,構(gòu)建精細(xì)化的備件生命周期管理,通過數(shù)據(jù)追蹤備件的實(shí)際可運(yùn)行周期,每年可節(jié)省數(shù)千萬的成本。
從以上這些視角看,設(shè)備維護(hù)工作由過去的強(qiáng)調(diào)為生產(chǎn)服務(wù),追求較高的設(shè)備完好率指標(biāo)轉(zhuǎn)變到以企業(yè)的經(jīng)濟(jì)效益為中心,要求設(shè)備管理工作重視維修費(fèi)用的管理與控制,找到以最少的維修費(fèi)用達(dá)到最高的設(shè)備可利用率的平衡點(diǎn)。企業(yè)的高層管理者如果能夠從“投資”的角度認(rèn)識(shí)維修和設(shè)備管理,將是十分寶貴的管理創(chuàng)新和理念轉(zhuǎn)變。
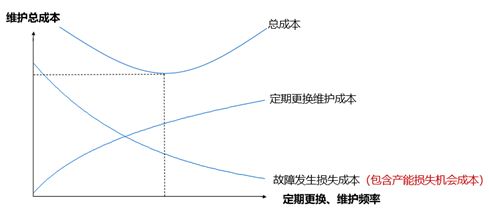
圖:設(shè)備管理的本質(zhì)是找到最佳維護(hù)平衡點(diǎn)
第五,想依賴“預(yù)測(cè)性維護(hù)”解決問題,忽視了基礎(chǔ)的數(shù)字化建設(shè)和數(shù)據(jù)積累
“預(yù)測(cè)性維護(hù)”一直是工業(yè)互聯(lián)網(wǎng)的熱門話題,聲稱通過物聯(lián)網(wǎng)和AI實(shí)現(xiàn)了預(yù)測(cè)性維護(hù)的公司繁多,工廠也期望將自己對(duì)設(shè)備故障的不確定性,交給 “預(yù)測(cè)性維護(hù)”來解決。但據(jù)筆者觀察,目前大部分此類項(xiàng)目仍是概念和實(shí)驗(yàn)性的居多,在可解釋性,可驗(yàn)證性、可復(fù)制性上都有問題。
預(yù)測(cè)性維護(hù)的落地比預(yù)想中困難,是因?yàn)槠髨D單純依賴數(shù)據(jù)提取可解釋的工業(yè)機(jī)理邏輯,難度遠(yuǎn)超想象。這里主要兩個(gè)原因:一是因?yàn)樵S多企業(yè)的基礎(chǔ)數(shù)據(jù)還缺乏積累,比如設(shè)備基本的巡點(diǎn)檢、維護(hù)保養(yǎng)、故障分析記錄,都還是散落在各種紙張、Excel中,設(shè)備缺乏數(shù)字化檔案,基本維護(hù)保養(yǎng)數(shù)據(jù)、備件更換記錄、故障和修理數(shù)據(jù),包括設(shè)備的故障特征數(shù)據(jù)還沒有結(jié)構(gòu)化的積累,就不可能實(shí)現(xiàn)模型的訓(xùn)練和驗(yàn)證。二是許多廠商企圖單純得依賴數(shù)據(jù)分析路徑而忽略了設(shè)備工程師現(xiàn)有專業(yè)知識(shí)和經(jīng)驗(yàn)的融入,光靠數(shù)學(xué)和AI算法容易走入統(tǒng)計(jì)陷阱,只是得到了相關(guān)性模型,不容易得出可解釋的因果性的預(yù)測(cè)模型。
總的來看,設(shè)備之于工廠,就像槍之于戰(zhàn)士。許多設(shè)備維護(hù)維修技術(shù)體系,也確實(shí)是從軍隊(duì)武器維護(hù)體系發(fā)展來的。構(gòu)建新型的設(shè)備管理能力,需要工廠管理者,認(rèn)識(shí)到設(shè)備之于工廠核心競(jìng)爭(zhēng)力的基礎(chǔ)性,積極變革促使設(shè)備管理和作業(yè)方式,向數(shù)字化、智能化發(fā)展。根據(jù)Gartner預(yù)測(cè),到2022年,60%以上的設(shè)備,將實(shí)現(xiàn)基于數(shù)據(jù)的智能運(yùn)維方式,設(shè)備智能化管理和運(yùn)維能力將會(huì)是衡量一個(gè)工廠核心競(jìng)爭(zhēng)力的重要標(biāo)志。最近國(guó)家工信部相關(guān)部門也正在起草和制定設(shè)備管理的國(guó)家標(biāo)準(zhǔn)、能力成熟度評(píng)估框架,將會(huì)對(duì)指導(dǎo)企業(yè)加強(qiáng)新型設(shè)備管理能力起到指引和促進(jìn)作用。